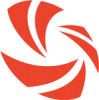
Coatings
The failure of gas turbine components can often result from high temperature oxidation, erosion, corrosion or a combination of these. To allow higher performance and longer life for these high cost, critical components they require additional protection due to the temperatures, stresses and wear they encounter in their daily use. ATL offers several different coating options to protect parts and extend their operating envelope and lifecycle, which can be applied to new manufactured or repaired components.
ATL has four surface coating booths. Two robotic air plasma booths, one robotic high velocity oxy fuel (HVOF) booth and one manual diffused coating spray booth.
Our robotic systems are capable of coating parts up to 250kg and 1200mm diameter with thermal barrier, abradable, wear resistant and/or water-resistant coatings. Our manual spray booth is temperature and humidity controlled with an integrated gas burner, allowing a pre-cure to be completed in-situ.

Our Coating Services
Diffused Aluminide
Wear Resistant Coatings
Robotic High Velocity Oxy Fuel (HVOF)
Robotic Air Plasma
NiCoCrAlY
CoNiCrAlY
MCrAlY Metallic Coating By Robotic HVOF
Ceramic Thermal Barrier Coating
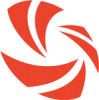
More Capabilities
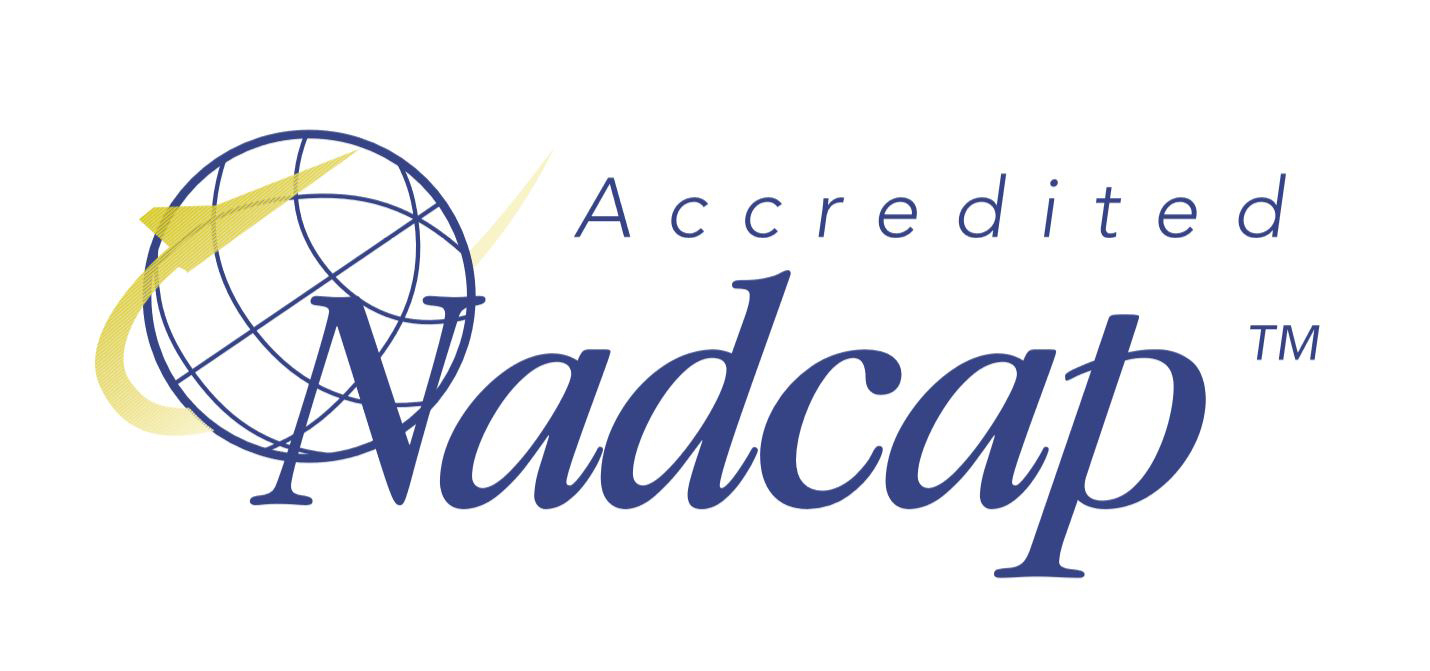



